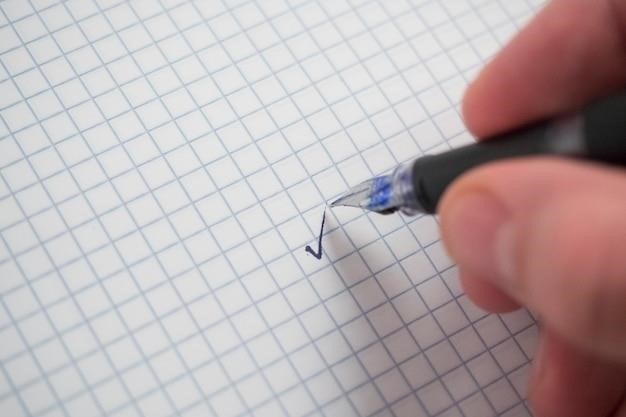
mig wire size guide
MIG Wire Size Guide⁚ Choosing the Right Wire for Your Welding Needs
This guide will help you choose the right MIG wire size for your welding needs. It covers factors like material thickness, welding process, desired penetration, and amperage capability. We’ll also look at common MIG wire sizes and provide a wire size chart for MIG welding.
Introduction
MIG welding, also known as Gas Metal Arc Welding (GMAW), is a versatile and popular welding process that utilizes a continuous wire electrode fed through a welding gun. The wire melts as it passes through the arc, forming a weld pool that fuses with the base metal. One of the key factors influencing the quality and success of a MIG weld is the choice of wire size. Selecting the right wire size ensures optimal penetration, weld strength, and overall efficiency.
Factors Influencing Wire Size Selection
Choosing the appropriate MIG wire size depends on a number of factors, each playing a crucial role in achieving the desired weld quality. Material thickness is paramount, as thicker materials require larger wire diameters to ensure sufficient penetration and a strong weld. The welding process itself, whether using solid or flux-cored wire, dictates the wire size needed for optimal performance. Desired penetration depth, a key factor in weld integrity, is directly influenced by wire size, with larger wires providing deeper penetration. Finally, the amperage capability of your welding machine must be considered, as it limits the maximum wire size that can be used effectively.
Material Thickness
Material thickness is a primary factor in determining the appropriate MIG wire size. Thinner materials, such as sheet metal, typically require smaller wire diameters, ranging from 0.023 to 0.035 inches, for optimal control and heat input. This prevents excessive heat from warping or burning through the thin material. However, thicker materials, like structural steel, demand larger wire sizes, often ranging from 0.035 to 0.045 inches, to achieve sufficient penetration and weld strength. Larger wires deliver more heat and filler metal, allowing them to melt through thicker base materials and create a robust weld.
Welding Process
The welding process you choose also plays a role in selecting the right MIG wire size. For instance, gas metal arc welding (GMAW), commonly known as MIG welding, often employs smaller wire diameters for thin materials, while thicker materials might require larger wire sizes. Flux-cored arc welding (FCAW), a variation of MIG welding that uses flux-cored wire, often uses larger wire diameters for increased penetration and weld strength, especially when welding thicker materials. Ultimately, the specific welding process dictates the optimal wire size for achieving the desired weld quality and performance.
Desired Penetration
The desired penetration depth of the weld is a critical consideration when selecting MIG wire size. Penetration refers to how deeply the weld metal fuses into the base metal. For shallow penetration, smaller wire diameters are often sufficient. However, when deeper penetration is required, larger wire diameters are typically used. This is because larger wires carry more heat, allowing them to melt a larger volume of base metal and create a deeper weld pool. The depth of penetration also affects the overall strength and integrity of the weld, making it a crucial factor in achieving the desired weld quality.
Amperage Capability
The amperage capability of your welding machine is another critical factor to consider when selecting MIG wire size. Amperage refers to the amount of electrical current flowing through the welding circuit. Larger wire diameters generally require higher amperage settings to melt the wire and achieve a proper weld. This is because larger wires have a greater cross-sectional area, requiring more electrical current to melt them effectively. Matching the wire size to the amperage capability of your machine ensures optimal welding performance and prevents overheating or overloading the equipment.
Common MIG Wire Sizes
MIG wire sizes are typically measured in thousandths of an inch (0.023, 0.030, 0.035, and 0.045 inches) or in millimeters (0.6, 0;8, 0.9, and 1.2 mm). The most common MIG wire sizes used in welding applications are⁚
- 0.023-inch (0.6 mm)⁚ Often used for thin materials like sheet metal and light-gauge steel due to its smaller diameter and lower amperage requirements. This size offers excellent control and fine heat input, perfect for delicate welds.
- 0.030-inch (0.8 mm)⁚ A versatile wire size suitable for a wide range of applications, including welding thicker materials like 1/8-inch steel. This wire size provides a good balance between penetration and heat input.
- 0.035-inch (0.9 mm)⁚ A popular choice for welding thicker materials, such as 1/4-inch steel, due to its larger diameter and increased amperage capacity. This wire offers deeper penetration and greater weld strength.
- 0.045-inch (1.2 mm)⁚ Used for welding heavy-duty materials and structural applications. This wire size provides the highest penetration and weld strength for thick materials.
0.023-inch (0;6 mm)
This wire size is commonly used for thin materials like sheet metal and light-gauge steel. It’s known for its smaller diameter and lower amperage requirements. The smaller diameter allows for precise control and fine heat input, which is crucial for welding delicate materials. It can also be used for more intricate welds where a larger wire would be too bulky or would risk melting through the material. The use of a 0.023-inch wire requires a welding machine that can handle the lower amperage range.
Here are some of the benefits of using a 0.023-inch wire⁚
- Improved control and precision during welding.
- Reduced heat input, minimizing the risk of warping or burning thin materials.
- Excellent for intricate welds and tight corners.
- Suitable for welding aluminum and other thin non-ferrous metals.
0.030-inch (0.8 mm)
This wire size is considered a versatile choice for MIG welding, suitable for a wide range of applications and material thicknesses. It offers a good balance between heat input and penetration, making it a popular choice for both thin and medium-thickness materials. The 0.030-inch wire size is commonly used for welding steel, aluminum, and stainless steel, making it a staple in many workshops. It’s also a great option for those new to MIG welding, as it provides a good learning curve and results in smoother welds.
Here’s why the 0.030-inch wire size is so versatile⁚
- Provides sufficient heat for welding medium-thickness materials.
- Offers good penetration without excessive heat input, minimizing the risk of warping or burning.
- Suitable for various materials, including steel, aluminum, and stainless steel.
- Offers a balance between control and welding speed, suitable for both beginners and experienced welders;
0.035-inch (0.9 mm)
The 0.035-inch (0.9 mm) MIG wire size is a popular choice for welding thicker materials and offers several advantages over smaller wire sizes. It’s often used for welding materials ranging from 1/8 inch to 1/4 inch thick, although it can also be used for thinner materials with proper settings and technique. The increased diameter of the 0.035-inch wire allows for greater heat input and penetration, resulting in stronger welds and a faster welding process.
Here’s why the 0.035-inch wire size is a good choice for thicker materials⁚
- Provides a higher deposition rate, making it ideal for welding thicker materials quickly and efficiently.
- Produces deeper penetration into the base metal, ensuring a stronger and more durable weld.
- Offers a good balance between heat input and arc stability, resulting in smoother and more consistent welds.
- Can be used for a variety of materials, including steel, aluminum, and stainless steel.
0.045-inch (1.2 mm)
The 0.045-inch (1.2 mm) MIG wire size is the largest commonly used in MIG welding and is typically used for welding materials thicker than 1/4 inch. It’s ideal for structural applications and heavy-duty welding due to its ability to deposit a large amount of filler metal and provide deep penetration. This size is also favored for multi-pass welding, where multiple layers of weld metal are applied to create a strong and durable joint.
Here’s why the 0.045-inch wire size is a good choice for thicker materials⁚
- Provides the highest deposition rate of all common MIG wire sizes, allowing for faster welding speeds and increased productivity.
- Produces deep penetration, ensuring a strong weld that can withstand high stresses and loads.
- Ideal for welding thick materials where multiple passes are required for a strong weld.
- Requires a higher amperage setting than smaller wire sizes, so ensure your welding machine has the capacity to handle it.
Wire Size Chart for MIG Welding
This chart provides a general guideline for choosing the right MIG wire size based on material thickness. It’s important to note that these are just recommendations, and the best wire size for your application may vary depending on factors such as the welding process, desired penetration, and the amperage capability of your welding machine. Always consult your welding machine’s manual and the wire manufacturer’s specifications for the most accurate information.
Remember to consider the type of wire (solid or flux-cored) and the welding process (MIG/MAG or gasless) when making your selection. Consult with a welding professional or refer to the wire manufacturer’s guide for more specific recommendations on wire type and size for your particular application.
Tips for Using Different Wire Sizes
When using different wire sizes, it’s essential to adjust your welding settings to achieve optimal results. Here are some tips⁚
- Thinner Materials⁚ For thinner materials, use a smaller wire size to avoid excessive heat input and potential burn-through. Adjust your welding speed and amperage to maintain a consistent weld bead and prevent warping.
- Thicker Materials⁚ For thicker materials, use a larger wire size to achieve deeper penetration and a stronger weld. Increase your amperage and adjust your travel speed to achieve a smooth, consistent weld bead;
Remember to practice with different wire sizes and adjust your settings accordingly to find the optimal combination for your specific application.
Thinner Materials
When welding thinner materials, it’s crucial to use a smaller diameter MIG wire to prevent excessive heat input and potential burn-through. This is because smaller wires deposit less heat, allowing for more precise control and reducing the risk of warping or distorting the material. Smaller wires also allow for a more refined weld bead, which is essential for thinner materials.
For instance, a 0.023-inch (0.6 mm) wire is often used for thin sheet metal or delicate components, while a 0.030-inch (0.8 mm) wire might be suitable for slightly thicker materials. Remember, the appropriate wire size depends on the specific material thickness and your welding machine’s capabilities.
Thicker Materials
When welding thicker materials, you’ll need a larger diameter MIG wire to achieve sufficient penetration and create a strong weld. Larger wires deliver more heat and melt a greater volume of metal, ensuring deep fusion into the base material. This is especially important for structural applications where the weld needs to withstand significant stress.
For example, a 0.045-inch (1.2 mm) wire is often used for thick steel plates or structural components, while a 0.035-inch (0.9 mm) wire might be suitable for medium-thickness materials. However, remember that the appropriate wire size depends on the specific material thickness, the welding process, and the desired penetration.
Considerations for Wire Type
The type of MIG wire you choose will significantly affect the welding process and the quality of your weld. There are two primary types of MIG wire⁚ solid wire and flux-cored wire. Solid wire is a single piece of metal, while flux-cored wire contains a core of flux that helps to stabilize the arc and protect the weld from oxidation.
Solid wire is generally suitable for welding thinner materials and requires a shielding gas to prevent oxidation. Flux-cored wire, on the other hand, can be used in applications where a shielding gas is not available or desirable. It also provides better penetration and weld quality in certain situations, such as welding dirty or rusty metal.
Ultimately, the choice between solid wire and flux-cored wire depends on your specific welding needs and the type of application.
Solid Wire
Solid wire is a single piece of metal that is fed through the welding gun and melted by the arc. It is the most common type of MIG wire and is generally used in applications where a shielding gas is available. Solid wire is known for its smooth and consistent welds, making it ideal for applications where a high-quality finish is required.
Solid wire is also available in a variety of alloys, each with its own unique properties. For example, ER70S-3 is a common solid wire that is suitable for general-purpose welding of carbon steel. It is also available in various diameters, ranging from 0.023 inches to 0.045 inches, allowing you to choose the right size for your application.
Solid wire is a versatile and reliable choice for MIG welding, and it is a good option for both beginners and experienced welders.
Flux-Cored Wire
Flux-cored wire is a type of MIG welding wire that contains a flux core. This flux core is a powder that melts and releases gases during the welding process. The gases protect the weld from atmospheric contamination, and the flux also helps to improve the quality of the weld.
Flux-cored wire is often used in applications where a shielding gas is not available, such as outdoor welding or welding in confined spaces. It is also a good choice for welding thicker materials, as the flux core helps to improve penetration.
Flux-cored wire is available in a variety of alloys and diameters, just like solid wire. The most common flux-cored wire is ER70S-6, which is suitable for general-purpose welding of carbon steel. Flux-cored wire is a good choice for both beginners and experienced welders, and it is a versatile option for a variety of welding applications.
Choosing the right MIG wire size is essential for achieving strong, high-quality welds. By considering factors like material thickness, welding process, desired penetration, and amperage capability, you can select the appropriate wire size for your application. Remember that thicker materials generally require larger wire sizes for deeper penetration.
Always refer to the manufacturer’s recommendations for specific wire sizes and welding parameters. With the right wire size, you can achieve consistent, reliable welds that meet your project requirements.
Whether you’re a beginner or an experienced welder, understanding the principles of MIG wire size selection will help you improve your welding skills and achieve better results.
Resources
For more detailed information on MIG wire sizes and welding techniques, consider exploring these resources⁚
- Arccaptain⁚ This website offers a comprehensive guide to MIG wire sizes and selection, covering various aspects of the welding process.
- Machineryhouse⁚ This supplier of engineering and metalworking machinery provides insights into wire diameters and their applications, as well as recommendations for welding capabilities.
- Bakersgas⁚ This website offers a detailed chart for choosing the correct wire size and type based on material thickness.
- Engweld⁚ This website provides a guide on choosing the right MIG wire size for various applications, including information on wire diameters and their suitability for different materials.
These resources can help you deepen your understanding of MIG wire selection and improve your welding skills.