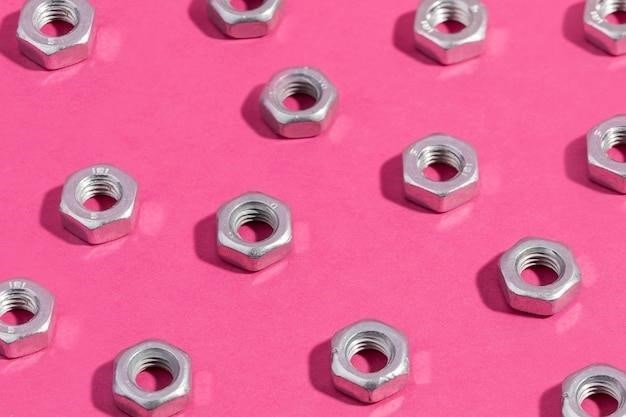
screw diameter guide
A screw diameter guide is a valuable tool for anyone working with screws, bolts, or fasteners․ It provides information on the various screw diameters, their applications, and how to choose the right screw size for your project․ This guide covers essential aspects such as understanding screw diameters, metric and imperial screw diameter systems, screw diameter measurement, screw diameter charts, screw diameter applications, choosing the right screw diameter, screw diameter and strength, screw diameter and compatibility, and concludes with a summary of the key points․
Understanding Screw Diameters
Screw diameter, often referred to as screw size, is a fundamental aspect of fastener selection․ It represents the width of the threaded portion of the screw, which directly influences its strength, holding power, and compatibility with mating components․ The diameter is typically measured in either inches (imperial system) or millimeters (metric system)․ Understanding screw diameters involves recognizing the different systems used, how they are measured, and the significance of diameter in determining the right screw for specific applications․
The first number in a screw size designation usually indicates the diameter․ For example, a screw labeled “M8” is a metric screw with a diameter of 8 millimeters․ In the imperial system, screw sizes below 1/4 inch are often represented by numbers (e․g․, #8 screw)․ The corresponding diameter for #8 is 0․164 inches․ For screw sizes above 1/4 inch, the diameter is expressed as a fraction (e․g․, 1/4 inch, 3/8 inch, etc․)․
The screw diameter is crucial for ensuring proper fit and function․ A screw that is too small may not provide sufficient holding power, while a screw that is too large may damage the material or create a loose fit․ Choosing the right screw diameter requires considering factors such as the material being fastened, the intended load, and the available hole size․
Measuring screw diameter accurately is essential for selecting the correct screw size․ Various tools can be used, including calipers, rulers, and thread gauges․ Calipers are particularly useful for precise measurements․ To measure the diameter, ensure the caliper jaws are properly aligned and positioned across the outermost points of the screw’s threads․
Metric Screw Diameters
Metric screw diameters are widely used throughout the world and are characterized by their dimensions expressed in millimeters․ The metric system provides a standardized approach to screw sizing, simplifying calculations and ensuring compatibility between different fasteners․ The designation of a metric screw typically starts with the letter “M” followed by the nominal diameter in millimeters․ For instance, an M8 screw has a nominal diameter of 8 millimeters․
The ISO metric screw thread family is a comprehensive system with a series of general-purpose threads․ It is based on a 60° thread angle and employs a standardized pitch, which refers to the distance between adjacent threads․ Common metric screw diameters range from M1 to M36, with smaller sizes often used for delicate applications and larger sizes suitable for heavy-duty fastening․
Metric screw diameters are classified into two series⁚ coarse pitch (indicated by the letter “C”) and fine pitch (indicated by the letter “F”)․ The coarse pitch series is typically used for general-purpose applications where a quick assembly is desired․ Fine pitch screws are often preferred for applications requiring greater precision and holding power, such as those involving thin materials or delicate components․
The metric screw diameter system is highly standardized, with specific tolerances and classes defined for different applications․ This standardization ensures interoperability and consistency, making it easier to select the right screw for a particular application․
Imperial Screw Diameters
Imperial screw diameters, often referred to as “inch” screws, are a system of screw sizing based on fractions of an inch․ This system originated in the United States and is still commonly used in North America․ Unlike the metric system, which uses millimeters, imperial screw diameters are expressed in fractions like 1/4 inch, 5/16 inch, or 3/8 inch․ The use of fractions can sometimes make calculations and conversions more complex, but imperial screw diameters are widely recognized and readily available․
The imperial screw diameter system is not as standardized as the metric system․ While it has established thread profiles and sizes, there are variations in thread pitch and other parameters․ This can lead to compatibility issues when using screws from different manufacturers or older systems․ For example, there are multiple thread standards within the imperial system, including Unified National Coarse (UNC), Unified National Fine (UNF), and Unified National Extra Fine (UNEF)․
Imperial screw diameters are often categorized based on their gauge․ Gauge refers to the approximate diameter of the screw head, with larger gauges indicating larger head diameters․ The gauge system is somewhat arbitrary, and the relationship between gauge and head diameter is not always precise․ However, it provides a general indication of the screw size and can be helpful for identifying screws when using older catalogs or reference materials․
Screw Diameter Measurement
Accurately measuring screw diameter is crucial for selecting the right screw for your project and ensuring a proper fit․ There are several methods you can use, ranging from basic tools like rulers to more precise instruments like calipers․ The choice of measurement method depends on the desired accuracy and the availability of tools․
For basic measurements, a ruler can be sufficient, especially when dealing with larger screws․ Simply measure the width of the threaded portion of the screw, excluding the head․ This measurement corresponds to the screw’s diameter․ However, for smaller screws or when greater precision is required, calipers are a more reliable option․
Calipers are specialized measuring instruments that provide precise measurements of internal and external dimensions․ For screw diameter measurement, use calipers to measure the width of the threaded portion of the screw, ensuring the jaws are properly aligned with the thread crests․ Calipers often display measurements in both metric (millimeters) and imperial (inches) units, making it easier to convert between the two systems․
When measuring screw diameter, it’s essential to be aware of the different types of diameter measurements․ Major diameter refers to the largest diameter of the screw thread, measured from crest to crest․ Minor diameter, on the other hand, refers to the smallest diameter of the screw thread, measured at the base of the thread․
Screw Diameter Charts
Screw diameter charts are invaluable resources for anyone working with screws, bolts, and fasteners․ These charts provide a comprehensive overview of screw sizes, their corresponding dimensions, and other relevant information, making it easier to choose the right screw for a specific application․ They typically include data on both metric and imperial screw systems, encompassing a wide range of screw types and sizes․
Screw diameter charts often include various parameters, such as the screw’s major diameter, minor diameter, thread pitch, and length․ They may also provide information on the screw head type, material, and thread class․ This comprehensive data allows users to easily compare different screw sizes and identify the most suitable option for their needs․
Many online resources and manufacturers offer downloadable screw diameter charts, making it convenient to access this information․ These charts can be printed and kept readily available for quick reference․ Some manufacturers even provide interactive screw diameter charts that allow users to filter results based on specific criteria, such as material or head type․
Using screw diameter charts can significantly simplify the process of selecting the right screw for a project․ They eliminate the need for manual calculations and ensure that the chosen screw is compatible with the intended application․ By consulting screw diameter charts, users can save time and effort while ensuring the success of their projects․
Screw Diameter Applications
Screw diameters play a crucial role in determining the strength, holding power, and compatibility of fasteners․ Choosing the correct screw diameter is essential for ensuring the success and longevity of any project․ Different screw diameters are designed for specific applications, each requiring different levels of strength and holding power․
For example, small screw diameters are commonly used in electronics, where delicate components require careful handling․ Larger screw diameters are typically used in construction and heavy-duty applications, where significant holding power and resistance to stress are necessary․ The choice of screw diameter is also influenced by the material being fastened․
Wood screws, often used for joining wooden components, typically have a larger diameter than machine screws, which are designed for metal applications․ The type of thread on the screw, whether coarse or fine, can also affect its application․ Coarse threads are generally used for faster driving and less-precise applications, while fine threads provide greater holding power and are suitable for delicate work․
Understanding the specific applications of different screw diameters is crucial for choosing the right fastener for the task at hand․ Consulting screw diameter charts and considering the material being fastened, the required holding power, and the overall project requirements are key factors in selecting the optimal screw diameter․
Choosing the Right Screw Diameter
Selecting the appropriate screw diameter is paramount for achieving secure and durable fastenings․ Several factors must be considered when choosing the right screw diameter for your project, ensuring the screw can effectively hold the materials together and withstand the intended load․ The material being fastened plays a significant role in determining the ideal screw diameter․
For instance, wood requires a larger diameter screw than metal to provide sufficient holding power․ The thickness of the material also influences the screw diameter choice․ Thicker materials require longer screws with a larger diameter to reach the appropriate depth and provide secure fastening․ Additionally, the type of thread on the screw can impact its suitability․
Coarse threads, while faster to drive, are less suitable for delicate materials or high-precision applications․ Fine threads offer greater holding power and are ideal for delicate work or situations where precise fastening is crucial․ The intended load and stress on the screw must also be factored in;
For applications requiring high strength and resistance to stress, a larger diameter screw with a higher tensile strength is recommended․ Consulting screw diameter charts and considering the specific application, material, and intended load will guide you in selecting the most appropriate screw diameter for your project․
Screw Diameter and Strength
The diameter of a screw plays a crucial role in determining its strength and load-bearing capacity․ A larger screw diameter generally translates to a stronger screw, capable of withstanding greater stress and tension․ This relationship stems from the increased cross-sectional area of the screw’s shaft, providing a larger surface area to distribute the applied force․ The material composition of the screw also significantly impacts its strength․
Screws made from high-strength materials like steel or stainless steel possess greater tensile strength and can withstand heavier loads compared to screws made from softer materials like brass or aluminum․ The type of thread on the screw also influences its strength․ Coarse threads, while offering faster driving, typically have lower tensile strength compared to fine threads․ Fine threads, due to their tighter spacing, provide greater grip and holding power, enhancing the screw’s overall strength․
The length of engagement, or the depth to which the screw is inserted into the material, also contributes to its strength․ Longer screws with greater engagement depth generally offer higher tensile strength due to the increased surface area in contact with the material․ Understanding the relationship between screw diameter, material, thread type, and engagement length is essential for selecting screws that can reliably withstand the intended load and ensure a secure fastening․
Screw Diameter and Compatibility
Ensuring compatibility between screws and their corresponding mating components is crucial for a secure and reliable fastening․ The diameter of a screw must be appropriately matched to the size of the hole it is intended to thread into, as well as the size of the nut or other fastener it will be used with․ Incorrect screw diameter can lead to loose fittings, stripping of threads, or even damage to the mating components․ A screw that is too small for the hole will not provide sufficient grip and may loosen over time․ Conversely, a screw that is too large for the hole will be difficult to insert and may cause damage to the surrounding material․
The thread pitch, or the distance between adjacent threads, is another critical factor in compatibility․ A screw and its mating component should have the same thread pitch for proper engagement․ If the thread pitches do not match, the screw will not fully engage with the mating component, resulting in a weak and unreliable connection․ Additionally, the type of thread, whether metric or imperial, must be consistent between the screw and the mating component․ Using a metric screw with an imperial nut or vice versa will lead to incompatible threads and a failed connection․ Understanding these compatibility factors is essential for ensuring a secure and lasting fastening․